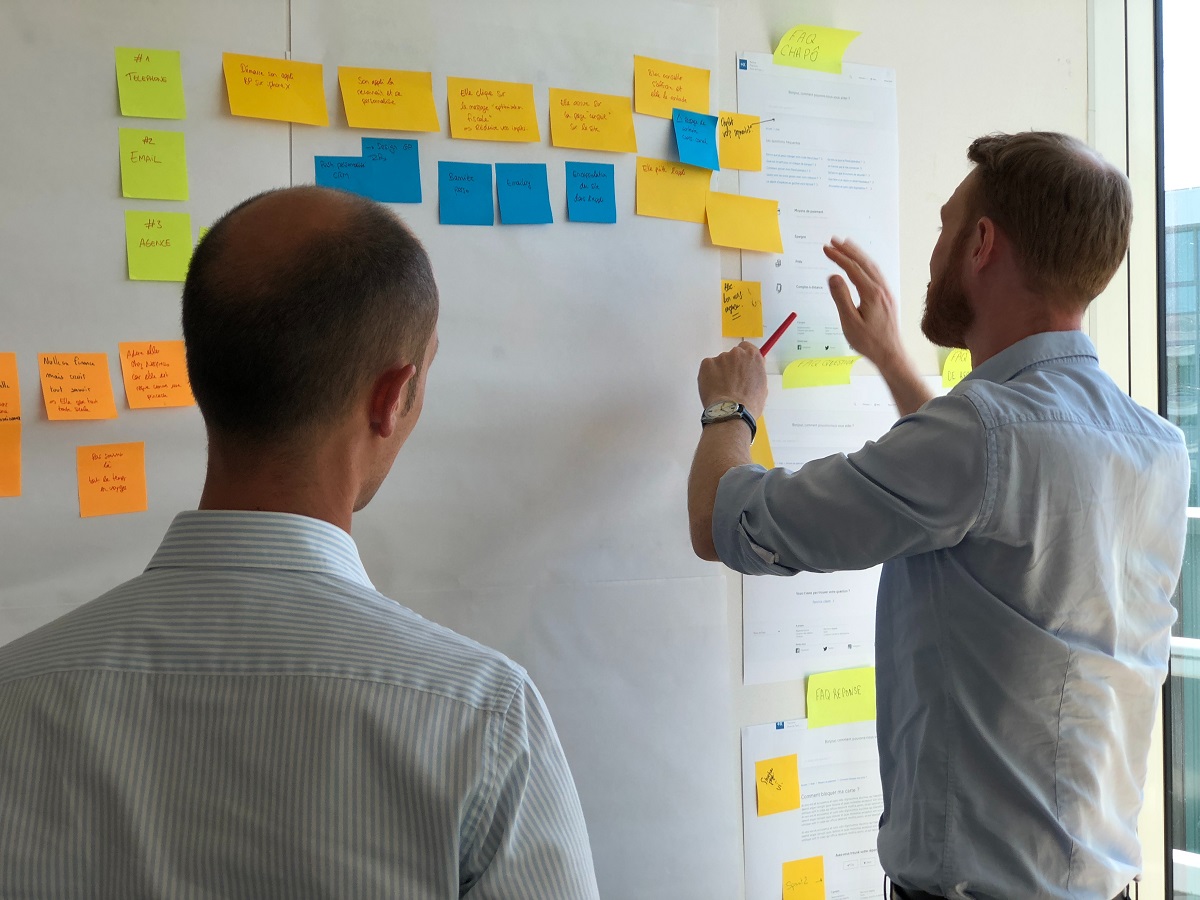
Industry 5.0
The European Commission’s Directorate General for Research & Innovation sees the core of Industry 5.0 as follows:
“Industry 5.0 recognises the power of industry to achieve societal goals beyond jobs and growth to become a resilient provider of prosperity, by making production respect the boundaries of our planet and placing the wellbeing of the industry worker at the centre of the production process.”
It states that:
“Industry 5.0 complements the existing Industry 4.0 paradigm by highlighting research and innovation as drivers for a transition to a sustainable, human-centric and resilient European industry. It moves focus from shareholder to stakeholder value, with benefits for all concerned. Industry 5.0 attempts to capture the value of new technologies, providing prosperity beyond jobs and growth, while respecting planetary boundaries, and placing the wellbeing of the industry worker at the centre of the production process.”
Industry 5.0 embraces Industry 4.0’s digitalisation and technology dimensions without its technologically deterministic nature.
Bridges 5.0 aims to build a theoretical and conceptual framework for Industry 5.0. Its objective in doing so is to enable the development of solutions for the workforce skills required in Industry 5.0, and will deliver guidance for the further work in the project. A first draft version appeared as an internal note1 and a final version is planned for publication by 1st January 2024.
Industry 5.0 connects (1) Human-Centricity, (2) Sustainability and (3) Resilience, which means;
- Putting human needs and interests at the centre, and adapting technology to the needs of workers.
- Reducing energy consumption, minimising waste and develop circular processes.
- Making industrial production and critical infrastructure robust by arming it against disruptions.
Industry 5.0 should in addition be socio-centric. The social context goes beyond human-centric workplaces, stressing the social function of cooperation and collaboration, and linking workplace, organisational, industrial and societal levels.
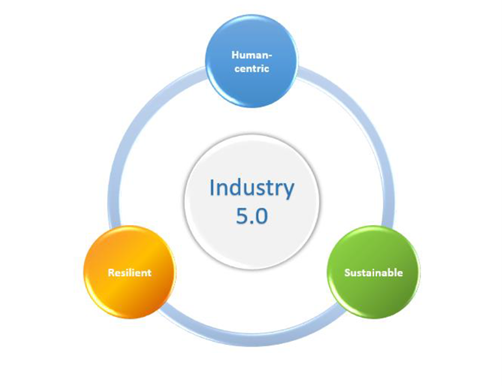
How do we arrive at understanding workforce skills in this context?
Industry 5.0 requires not only changes in knowledge and skills but also in the engagement of the workforce. Knowledge is the “set of know-what”, skill is the “ability to carry out managerial or technical tasks” (know-how), and engagement is the “cognitive and relational capacity”. When we talk about skills, a useful distinction can be made between:
- Foundational skills such as literacy and basic digital skills, necessary for many jobs in the digital age.
- Job-specific skills, necessary for a specific profession or function; this includes specific social and interactive skills (which, for example, differentiate hairdressers from software programmers).
- Industry 5.0 skills related to human-centric, resilient and sustainable behaviours and practices.
The human-centric aspect of Industry 5.0 represents a change in the strategic orientation and mindset of industrial companies, mainly from profit maximisation towards increased responsibility for society and the people within the organisation.
The following demands are put on the workforce:
- Dealing with human-centred technologies, and
- Dealing with empowerment and participation.
Technology that aims to be human-centric needs to factor human-centredness into its design, introduction, use and outcomes. Technology, if it does not replace or control humans, should augment their capabilities. Augmenting technologies or assistance technologies have the purpose of supporting people in their work and making work easier. Such technologies offer a means to address shortages of skilled workers by increasing the number of potential workers. Collaborative robots, or augmented and mixed reality (AR/MR) solutions, are increasingly being introduced, especially in industry. The requirement is that the workforce is able to work with these technologies.
The adoption of technology by the worker further depends on the usage of the technology and the quality of work results. Optimal use of technology requires the decentralisation of decision-making and empowers workers to have more autonomy in decision-making. The workforce not only needs to understand technology in all its forms, it needs to understand how to co-determine the shaping of the Industry 5.0 workplace. Participation is core to human-centric technology and work, and relates to democratisation of the workplace. Thus, Industry 5.0 indirectly supports the autonomy and needs of workers.
Sustainability is perhaps the least concrete and tangible of the three workforce skills. To develop sustainable manufacturing systems needs coordinated effort in many areas (product, process, technology, organisation, skills, mindset, leadership approach etc.) along the whole value chain. Reaching the UN Sustainable Development Goals means engaging the European workforce in green tasks, jobs and skills. Green jobs are of two of kinds: (i) jobs in businesses that produce goods or provide services that benefit the environment or conserve resources; (ii) jobs in which workers’ tasks involve making their establishment’s production processes more environmentally friendly or using fewer natural resources. The goal of sustainability addresses specific changes in policymaking and at all levels in ecosystems. Reaching net-zero emission targets requires a fundamental change in attitudes and behaviours in the workplace, companies, industry and society. The workforce must adopt sustainable behaviours that allow them to make the right judgements in their work. The input of everyone is needed to avoid unnecessary emissions, to change personal behaviours (for example, travel and consumption) and to deal with the complicated trade-offs that will arise.
Resilience points to anticipation skills. Resilience is, partly, the capability to anticipate (external) shocks and/or crises. In striving towards resilience there is an inherent trade-off between efficiency and redundancy. Efficiency in the form of outsourcing, downgrading, saving resources, saving costs, streamlining structures etc., may lead to lock-ins and rigidities, and in the face of a shock, lead to vulnerability and disruption. In contrast, redundancy is perceived as inefficient in periods of non-crisis from a short-term perspective. Yet acceptance of redundancy may be an enabler of longer-term flexibility and efficiency. Resilience is also the skill to manage disruption, to bounce back to stable functioning, and on top of that to bounce forward, i.e. learn from the past, conceptualise shocks as an opportunity to evaluate options, and embrace (radical) change (creative destruction). Workforce resilience skills include how to understand and anticipate shocks, and how to develop strategies to deal with those shocks, understanding the need for redundancy from a longer-term perspective.
Activities of Bridges 5.0
In order to pin down the workforce skills associated with I5.0, Bridges 5.0 undertakes a number of activities. The most salient are the Teaching Factory Lab and the Learning Factory Lab where practical implementations of new technology and skills will be studied (see the following article in this Newsletter.
The challenge is to understand how companies, businesses and organisations transform themselves to implement human-centricity, sustainability and resilience, and to assess what this implies for the concrete design of jobs, tasks and workforce skills.
2 Comments
Leave A Comment
Related articles
March 24, 2025
March 23, 2025
March 11, 2025
We should be careful about the terminology and move beyond the ‘skills’ and ‘jobs’ agenda. Future employment requires knowledge and competences, not just skills and employment is more long term than just a short term ‘job’. Also ‘resilience’ suggests just putting up with the current situation, and that is certainly not compatible with empowering the workforce and a more human-centred approach.
Dear Linda. Thank you for your response. Our intention is indeed to integrate a longer term perspective. We eventually want to understand what Industry5.0 implies for firms that actually perform human-centric, resilient and sustainable. And, subsequently, what are the consequences in terms of the deployment of people, the deployment of technology, and the firm deals with resilience and sustainability. We do not only look at skills and jobs, but also to what this means for qualifications and the division of labour, the type of organisational structure (production systems) and approach of management / leadership. Eventually we connect these insights with the notion of EDI as well, that is, try to assess what Industry5.0 behaviour means for industries / ecosystems and society. We welcome your thoughts (and those of others).