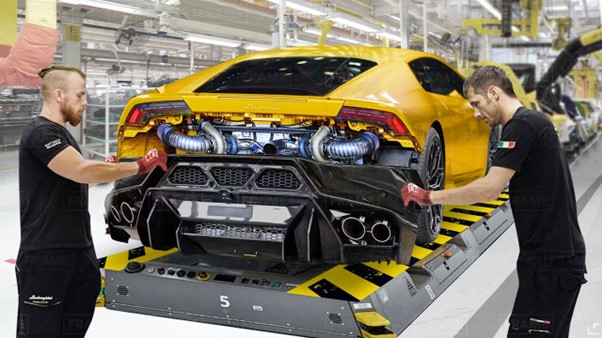
Lamborghini factory, Sant’Agata Bolognese, Italy (Source: Youtube)
In June 2023, Bridges 5.0 partner Valeria Cirillo and her colleagues at the University of Bari (Italy) published an article on trade union responses to the adoption of new technologies. Peter Totterdill talked to her about the article and its implications for Industry 5.0.
Peter: Please introduce yourself and your role in the BRIDGES 5.0 project.
Valeria: I am Associate Professor in Economics at the Department of Political Sciences of the University of Bari ‘Aldo Moro’. Additionally, I am affiliated with the Institute of Economics of the Sant’Anna – School of Advanced Studies (Pisa, Italy) and serve as a board member of the PhD school in Economics at Sapienza University of Rome. Within BRIDGES 5.0, I serve as the scientific coordinator of the UNIBA team. Our specific contribution lies in Work Package 2, where we aim to assess the nature of job transformations in the context of the so-called 4th industrial ‘paradigm’, with a focus on the adoption and use of ‘Industry 4.0’ technologies related to digitisation, automation and interconnection. We aim to examine the consequences related to task restructuring, emerging occupations, skill needs, shortages, and gaps. To delve into these aspects, we contribute to regional-level analyses and conduct firm-level statistical elaborations relying on Italian employer-employee data.
Peter: When and why did you become interested in trade unions’ role in Industry 4.0?
Valeria: Over the years my research has concerned labour market dynamics with respect to technological change. In this respect, institutional factors play central role in defining the paths of technological change and in shaping its impacts on occupations, jobs and the reconfiguration of tasks. ‘Institutions’ mean analysing the role of the State – through industrial and active labour market policies – but also dissecting collective bargaining between social actors and exploring divergences in terms of interests and power relations. Technologies, but more generally choices about which technologies to develop and adopt, are not neutral. It follows that the consequences for the world of work are not neutral either. From this perspective the effects of technological change tend to unfold asymmetrically between employment and the remuneration of labour and capital, between social groups, firms, geographical areas. This is because the adoption of a specific technology within firms depends, among others, on two important factors: the complex interplay between knowledge and firm capabilities and the distribution of power between capital and labour.
The latter means that technological change reflects existing power relations, contributes to their evolution and has major consequences for the distribution of income. It is therefore not a deterministic and neutral process, but has a social and political dimension. From this perspective, analysing how and to which extent trade unions are involved in the current wave of adoption of digital and automation technologies – defined as Industry 4.0 – is of paramount importance.
Peter: What are the principal questions you are seeking to answer in this study?
Valeria: Our paper, titled ‘Trade Unions’ Responses to Industry 4.0 Amid Corporatism and Resistance’ published in PSL Quarterly Review – is grounded in intensive fieldwork conducted from 2016 to 2018 in a selection of Italian metal companies. (The study of these companies was part of a larger research programme promoted by the Claudio Sabattini Foundation, commissioned by FIOM-CGIL, one of the leading Italian TUs, and involving researchers from several universities and research institutes. The main purpose was to understand characteristic trends concerning the organisation of work and working conditions occurred in recent years alongside the introduction of technological practices related to I4.0.) The study involved semi-structured interviews with workers, managers, IT specialists, and trade union delegates. The primary objective was to enhance understanding of the role played by trade unions in the process of technological change. We specifically distinguished between the ‘design phase’ of technologies and the ‘implementation phase’.
To address these questions comprehensively, we examined the extent to which trade unions were involved in the organisation of work and assessed their attitudes toward the ongoing transformation. The selection of these areas of analysis stemmed from our keen interest in the effective role of trade unions when confronted with technological and organisational transformations. Additionally, we aimed to explore emerging dichotomies, such as participatory versus conflictual practices and the actual role of union delegates when ‘bargaining over technologies’ (whether serving as a transmission channel for managerial decisions or advocating for collective workers’ claims).
Peter: In the article, you discuss “managerial corporatism” and how it can undermine the capacity of organised labour to pursue its own interests against those of the employers. Some researchers such as Tony Huzzard discuss the potential co-existence of “Boxing and Dancing”. Do you think there are conditions under which unions can negotiate ‘win-win’ outcomes without undermining their essential focus on workers’ interests?
Valeria: Yes, in theory if trade unions were involved in the development/design of the technologies and if they were used to improve working conditions in a broad sense, it would be possible to have a win-win outcome. Our analysis showed that TU’s negotiating role was significant during the phase of technological implementation (e.g. by opposing the introduction of intrusive forms of workers’ surveillance) and related organisational change. However, in all cases studied, we detected some important limits to the underlying bargaining process (e.g. in the absence of negotiation over internal working times and saturation) and a lack of the involvement of TUs in the design phase of I4.0 artefacts, regardless of the degree of digitalisation and robotisation in progress. In the research we have identified two alternative responses by TUs to the introduction of Industry 4.0 technologies, either reactive/conflict-oriented or proactive/corporatist-oriented. Interestingly, the higher the level of technological innovation already present, the higher the degree of union participation in the deployment of such technologies.
A proactive/corporatist-oriented attitude applies in particular to Ducati and Lamborghini. At Lamborghini, the role of TUs is considered fundamental, even by white-collar workers, when introducing technological innovations. Indeed, this circumstance may have been inherited by their shared parent company, Audi, which is known to introduce a “workers chart” defining the standard of work organisation in all its subsidiaries. However, this is coupled with the pre-existing system of industrial relations typical of the Bologna area. This led one of the interviewees (Technologist, Lamborghini) to say that, “Without support from the trade union, nothing can happen here. Neither organisational, nor technological change”. On the other hand, a more reactive/conflict-oriented attitude was discovered at Cesab-Toyota and Bonfiglioli, where TUs displayed a lower degree of participation in managing the process of technological adoption.
Peter: You say that “I4.0 represents a chance to rejuvenate a sterile bargaining system, creating a new role for TUs as transmission channels of managerial decisions and as facilitators for digitalising the work process at the plant level”. How does this work in practice?
Valeria: This is part of the so-called ‘functionalist approach’, a current branch of studies highlighting that Industry4.0 represents a major chance for Trade Unions to gain a new position in the system of industrial relations. For instance, this may happens through decentralised collective bargaining and second-level agreements regulating many aspects of the organisation of employment contracts (working hours, internal and external working times, specific leaves for education or parental care issues). In the case of Germany, a recent study by Haipeter focussing on the relationship between I4.0 and work councils in the manufacturing sector foresaw a series of new actions on behalf of TUs based on the activation of work councils and on cooperation between employers and delegates. Given that the founding pillars of I4.0 may pose serious challenges for unions in terms of employment stability, work organisation, deskilling processes, and working conditions, it has been recognised that conciliatory and collaborative practices are indeed required. This project, dubbed “Work2020” envisages a new strategic role for work councils, ranging from consulting with the company (identifying dissemination and new forms of digitisation), to strategy, defining problems and domains of analysis and marketing, as well as promoting plant level agreements.
Peter: If, as you say in the article, “the complete transformation of TUs is envisaged”, do unions need to build new competencies to deliver this role? What lessons can be drawn from the “Work2020” programme in Germany?
Valeria: As said before the Work2020 project outlines a significant level of involvement from workers’ delegates concerning the organisation of work and degrees of power and hierarchies at the plant level, technological adoption and implementation, occupational training and working conditions. Overall, the workplace significantly increases its importance as a locus of negotiation in Germany. Similar efforts were made in Italy to shift collective bargaining from the national/sectoral level towards individual firms. This requires a ‘proactive’ approach from work councils toward digital transformation as well as an institutional level of worker participation through the implementation of practices devoted to training workers’ representatives.
Peter: Why is the ‘Italian Motor-Valley’ of specific interest in relation to Industry 4.0?
Valeria: We chose companies in this area because it constitutes a distinctive technological district situated in the outskirts of Bologna, specialising in the engineering and automotive industry. The rate of adoption of digital and automation technologies in this region is notably higher compared to other areas of the country.
Peter: Please describe the context of the ‘Italian Motor-Valley’ in terms of industrial relations.
Valeria: This geographical region has been historically crossed by a twist of conflictual and participatory practices which led, in the early 1990s, to the formalisation of technical bilateral commissions on work organisation which are still present. Overall, however, the Italian system of industrial relations was characterised by the absence of bargaining over the organisation of the work process and technological innovations. In this respect the ‘Italian Motor-Valley’ was quite an exception.
Although three out of four establishments belong to non-Italian parent companies, strong trade union organisation was present well before the change in ownership, as testified by the history of industrial relations in the Emilia-Romagna region (where Bologna is located). FIOM has been quite strong here since the 1960s, the period of Italy’s “Hot Autumn” of industrial relations. In addition, all the firms studied are characterised by second-level bargaining, developed under comparable negotiation agreements undertaken by the local FIOM-Bologna.
Peter: How would you summarise the role of trade unions in shaping work organisation in the four companies?
Valeria: In terms of organisational change, our research material points to the role of four relevant domains of analysis with respect to work organisation: training activities, general high-performance work practices (HPWPs), career paths, and evaluation procedures. In all contractual agreements, TUs have obtained the formal recognition of educational achievements, such as diplomas, bachelor’s and master’s degrees. This recognition consists both of monetary awards and time off to attend class.
With respect to informal, on-the-job training, at Cesab-Toyota and Bonfiglioli, no mention appears in the contract, while at the two ‘Audi’ firms – Ducati and Lamborghini – specific internal training programs and even dedicated places on the factory floor have been created. Additionally, in the latter firms, TUs have been active in launching and promoting internship programs aimed at young students. Many interns complete a training period and are later hired by the company. This initiative, known as DESI (Dual Education System Italy) is the result of the typical German vocational training system as well as regional and state initiatives promoting active educational programs. This is indeed good practice.
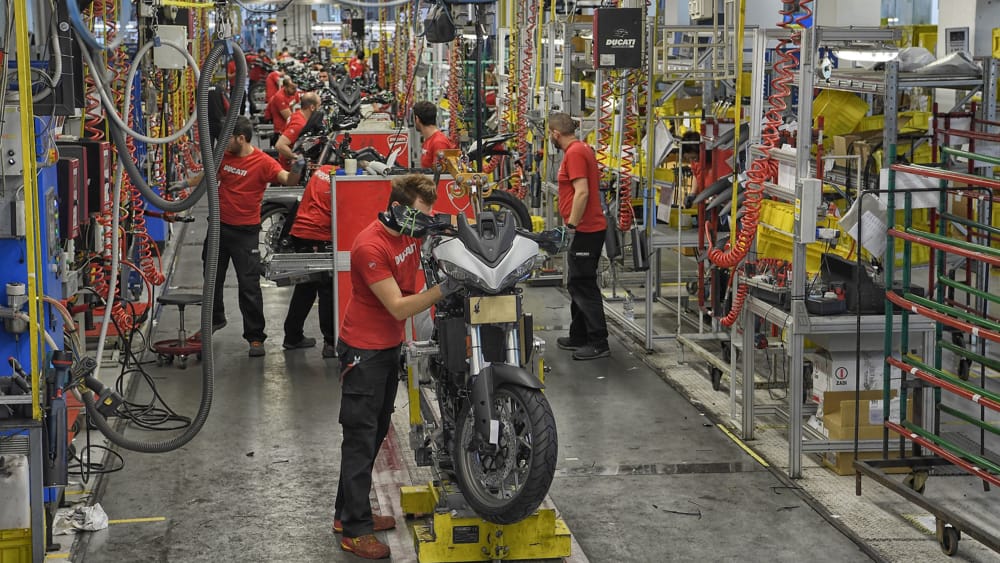
Ducati factory (Source: Racing World)
The deployment of HPWPs – namely job-rotation schemes and participatory practices such as suggestions for improvement, team meetings, teamwork, and kaizens – varies across firms, from widespread and generally formalised to informal and scattered activities. In general, organisational practices stand at the core of TU negotiations when drafting the content of the contractual agreement, as demonstrated by the existence of a technical bilateral commission on “work organisation”. For instance, TUs at Ducati are pushing to obtain transparent and formalised criteria when acknowledging operators’ versatility and multifunctionality, which arise when operators are able to execute tasks at different phases of manufacturing. Continuous improvement systems are established at Lamborghini, while lean practices such as asaichi and andon are present in Cesab-Toyota.
When HPWPs are less formalised or still in development, as is the case of Bonfiglioli, TUs seem to lack the ability to intervene, and their influence is limited. For instance, job-rotation practices have been acknowledged as important by managers at Bonfiglioli, but their implementation has not been shared with workers. It appears that the negotiation phase can start only after the organisational decision has already been taken. The negotiation of assessment procedures and career paths is characterised by a more passive role of TUs at Cesab-Toyota and Bonfiglioli, while a more active role characterises TUs in the two German cases. One distinctive element is the introduction of the Audi workers chart, which is helpful in formalising the latter’s schemes, at least in the contractual agreement.
All case studies show a generalised intensification of working time. Takt-time and dead time have been generally reduced. This is the result of the introduction of the just in time principle of production and of the general tendency to keep the production flow ‘tense’. Although there is no explicit mention of the issue of saturation of working time in the contractual agreement, at Bonfiglioli there is a process of information sharing between the timekeeping department and assembly line workers: times and methods of execution, when introduced for the first time, are formally explained to the workers involved in a given assembly line, with the presence of TU delegates.
Peter: What is constraining the ability of unions to influence the organisation of work?
Valeria: Overall, TUs have demonstrated some ability to negotiate on technological implementation. Indeed, TUs acknowledge the underlining threats of deskilling related to the introduction of I4.0 technologies. The introduction of new technological systems has implications for the organisation of labour, especially when it comes to increasing production saturation. The goal is something akin to the “Elementary Technological Unit” of FIAT (an Italian automotive manufacturer), the latter being characterised by the proceduralisation and fragmentation of complex activities into simple tasks, therefore exposing workers to the possibility of substitution. In the words of an interviewee ‘As a TU, we lag in the analysis of organisational flexibility and the consequences on contractual practices. From the point of view of the effects, we have tried to limit the social control of the worker, from surveillance to performance evaluation, without objecting to the introduction of technology’ (TU delegate).
Peter: How involved have unions been in the introduction of I4.0 technologies, and with what consequences?
Valeria: When we focus on the recent wave of technological change, the number of empirical contributions is smaller due to the lack of adequate quantitative data and the specificities of I4.0 adoption within a few large companies. In a recent work – based on Italian micro data – we have highlighted the overall scattered adoption of I4.0 technologies. The presence of company-level agreements is positively associated with investments in I4.0, mainly in manufacturing and SMEs. However, the data does not provide information on the role of TUs in the bargaining process of new technologies, nor does it provide details on the content of second-level bargaining. Therefore, we came up with the idea of a qualitative research analysis.
Concerning our cases, in terms of TU’s role in influencing the process of technological change in the design phase, we observed that TUs demonstrate a general acceptance of the ongoing process of transformation. They seem to play little role in the design phase overall (e.g. no interaction with the R&D department) and tend to consider technology as a given. One might ask whether it is legitimate to require TUs to intervene in the phase of technological design which, arguably, should be firmly in the hands of the management. Nonetheless, TUs have rather been pivotal in influencing the process of technological adoption at the macro scale. Indeed, they exert a crucial role in promoting huge investment plans involving complete technological upgrading, together with the development of new products. This seems to have occurred in all our firms except Cesab-Toyota. At Lamborghini, TUs have been able to obtain an investment plan of 50 million euros to locally manufacture a brand-new SUV model (known as URUS) instead of at an Audi plant in Bratislava, Slovakia.
TUs have also played a major role in promoting investment in innovation and new product lines at Ducati. Overall, whenever technology assumes its labour-augmenting nature, say, whenever it entails expansionary investments, construction of new productive capacity, elimination of old vintages and new product lines, TUs have manifested a clear proactive role in the firms under study.
Their role in the implementation phase is even more pronounced. In fact, TUs recognise the importance of participating in this process, as demonstrated by the presence of technical bilateral commissions called “New Products and New Processes”. These commissions are a typical, long-lasting trait of trade union organisation in Emilia Romagna. Within all firms, technical bilateral commissions are either established to oversee work organisation and technology or explicitly mentioned in contractual agreements to be activated later on. By means of the active role exercised within these commissions, TUs have explicitly reacted to the adoption of I4.0 technologies. For example, at Bonfiglioli, a contractual agreement explicitly set limits on the use of MES (Manufacturing Enterprise System) software, ruling out the possibility of collecting data on individual rhythms of production and individual performance, and their use for disciplinary purposes.
Peter: Can you summarise ‘good practice’ in union strategies as they negotiate around I4.0?
Valeria: Our study reveals that even in the absence of a strong corporatist culture, trade unions can improve working conditions and direct technical change towards more inclusive and less predatory methods of implementation. Indeed, trade unions should not forget their institutional macroeconomic role in counterbalancing inequality and hierarchies, and in guaranteeing not only workers’ rights, but also social rights as a whole. The implementation of the DESI (Dual Education System Italy) program that I mentioned before, is good practice in negotiation. The reaction of TUs in Bonfiglioli of ruling out the collection of data on individual rhythms of production and individual performance, and their use for disciplinary purposes, represents another good example.
Peter: Are there wider lessons as we move to Industry 5.0?
Valeria: It would be desirable to observe the enhanced participation of trade unions in shaping technological choices, extending beyond their typical involvement solely in the implementation phase (as our research highlighted). Moreover, a more active role from public actors in establishing dedicated infrastructures for collecting the vast amount of data generated by new technological artifacts would be beneficial. It is crucial to ensure that this data does not solely flow into additional private platforms controlled by major tech companies, upon which many firms often depend.
Peter: Thank you for these very valuable insights Valeria.
Related articles
March 24, 2025
March 23, 2025
March 11, 2025