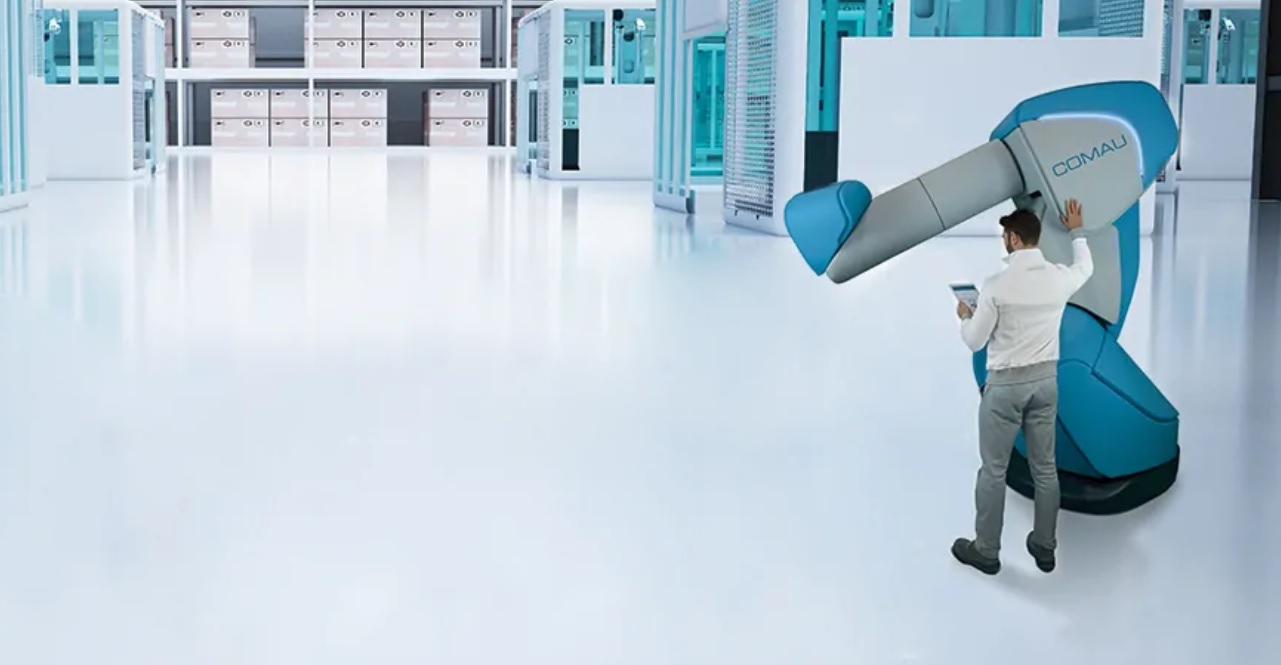
Innovation in manufacturing processes is a slow but continuous state of transformation. Advancing robotics solutions combined with digitalisation and fast communication technologies, are changing the entire manufacturing panorama.
In this evolving scenario, human–robot and human-digital technologies collaboration will become a major aspect of future smart factory. Think, for example, of the impact of Generative Artificial Intelligence on shopfloor activities. Collaborative robots and digital technologies are predicted to be key elements in transforming today’s factory into the human-centric, resilient, and sustainable factory of the future. However, despite all these technological advances in robotic and digital technologies, humans will continue to play important roles in today’s factory and those of the future because of their distinctive skills. For sure, as more technologies are available and ready to be implemented in manufacturing, more interactions between digital technologies and humans as well as robots will occur.
The successful implementation of all these technologies in the production environment requires specific consideration of human factors, and in particular the involvement of all stakeholders in the redesign of new production process and workplaces with the introduction of new technologies.
Much research has been conducted concerning the dynamics that influence the adoption of a new technology or service. For example, theory suggests that predictors of the intention to adopt a wearable healthcare device are (1) interpersonal influence, (2) attitudes toward a new technology, (3) self-efficacy, (4) personal innovativeness, (5) specific technology domain interest, and (6) perceived expense (Lee & Lee, 2018).
The research on this domain found that an individual’s attitudes have a significant influence on new technology adoption based on human-technology collaboration. This result leads to the conclusion that if a new technology or solution, for example based on human-technology collaboration, has been adopted by only a few individuals within a factory, then the new process using this new technology or solution would carry a high level of uncertainty about its final, successful adoption. The research assumes that is mainly because there is little information about the new technology or solution, especially in terms of understanding its usefulness for final users, (e.g. the workers). The adoption of a new technology or solution in a flexible production system often means an increasing cognitive workload and psychological strain for assembly workers, resulting in potential errors during assembly. Even if the decision to adopt smart factory technologies is an organisational decision, workers’ trust in the use of the new technologies and their impact on work organisation is mediated between performance expectancy, facilitating conditions, and company behaviour.
Nevertheless, this significant and positive role of attitudes and trust suggests that if attitudes and trust toward new technologies or solutions could be changed, then there would be more individuals who would adopt them in a conscious and informed way. It is, therefore, important to support workers in the new technology implementation and adoption process.
User‐centered development and design processes are described, for example, in many research works (Kluge & Termer, 2017) (Pokorni, Zwerina, & Hämmerle, 2020).
Our first application of user centered design started in 2016. We set up a user centered design approach made by design sprints. In particular, we argued that an inclusive human‐centered design and development approach would be particularly suitable to change attitudes in the context of wearable devices involving workers and engineers.
We used the Design Thinking methodology to support our Manufacturing Innovation process with the following pillars:
- Place the end-user, in our case the workers, at the centre.
- Include the end-user in the design team as a central element of the project.
- Consider the end-user as the unique and only real expert in the system.
The fundamental step toward this change of attitude and building trust towards the new technology was to train workers in using the design thinking methodology and to transform them into observers and designers.
We started from the consideration that in a factory there are lot of things that can be implemented and enhanced, including interfaces, devices, communication systems, internal flows and paths. But who knows every element or single task within a factory? ‘Workers’ is the answer, who are also USERS within a design process.
That’s why in our discussion we agreed that if we train users, they will be the best possible observers and designers.
The innovation process was arranged in three sprints:
- TRAINING DESIGN THINKING
We arranged a training workshop with the workers and the manufacturing process engineer to:
- Transfer Design Thinking Tools.
- Train and allow workers to make direct observation.
- Start a macro concept generation.
The workshop started with the challenge: How to perform all the necessary traceability operations required during the assembly task using a device that is portable and without relying on the current system and device?
- DIRECT OBSERVATION
We managed two weeks of USERS observation on the production line with the objectives of finding and describing the main:
- Actions.
- Phases.
- Positive elements.
- Critical elements.
- Timing.
- ANALYSIS OF OBSERVATION RESULTS AND CONCEPT REFINEMENT
We managed a workshop to highlight progress and refinements emerging from the initial concept after the direct observation sprint. The workshop objectives were to:
- Share the results of the direct observation.
- Share a presentation of the advanced concept.
- Define a first experience of use on the mock-up.
This approach was used in several sessions, generating new ideas and solutions. One of the most important aspects that emerged from the different experiences was the overall satisfaction of the participants. First of all, the level of satisfaction of the workers involved. As well as having learned the fundamentals of Design Thinking, the workers were able to actively contribute to the conception and design of the solution they would have to use. This also allowed the workers to share the first results with other colleagues during the direct observation phase, identifying other possible critical points and improvements. The diverse team comprised tech experts and less experts, early adopters and sceptics, all working together. Furthermore, it allowed workers to improve the process of understanding the advantages and benefits of using new technologies, thus removing attitudinal barriers and lack of trust regarding the final goal of adopting the new technology.
At the end of each workshop, we received a lot of positive feedback from the participants. For example, some common positive comment that we’ve received from the final users were:
- “For the first time we felt like protagonists in designing a solution that we had to use. We always use solutions designed on our presumed needs that did not take potential problems into account during the real usage.”
- “I believe that the choice to have the users design the portable device was a farseeing choice also for future projects”.
- “I worked to make it easier to do our job by having someone else do it, the ‘technology’”.
- “Unique experience because it is the user who designs new solutions and not the designer”.
- “A unique experience where the worker is taken into consideration and his needs are listened to”.
We also received positive feedback from the company, especially for the inclusive approach. In fact, workers involvement results in a minor risk of rejection for the new solution adoption and a reduction in design efforts to reach the final solution in line with the final user expectation.
Related articles
May 11, 2024